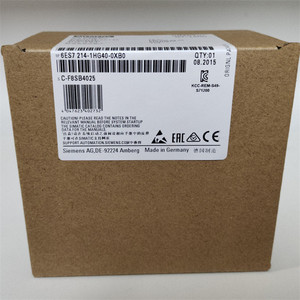
PLC Controller 6GK1411-5AB10 Siemens IE/PB LINK PN IO Ethernet Communication Processor
$300.00 - $800.00
Min Order: 1 piece

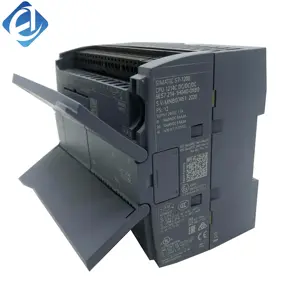
New Original 6ES7214-1HG40-0XB0 6ES7 214-1HG40-0XB0 S7-1200 S7 1200 PLC Module Stock In Warehouse
$198.00
Min Order: 1 piece

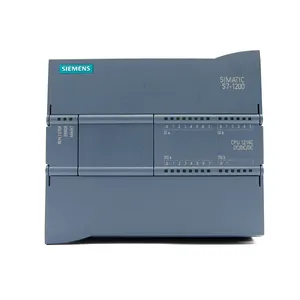
6ES7 214-1ad23-0xb0 6ES7214-1AG40-0XB0 S7 1200 Control Unit Siemens Simatic Plc Programming Controller S7-1200 Cpu Plc Price
$76.00 - $82.00
Min Order: 1 piece


New Original PLC To Micro PLC With A USB Port Mitsubishi FX3SA PLC Programmable Logic Controller
$50.00 - $200.00
Min Order: 1 set


Manufacturer Reasonable Price Small Plc Controller Control System Plc for Plastic Injection Machine Codesys Plc
$68.57 - $171.43
Min Order: 1 piece

Haiwell PLC H60S0R high speed PLC controller for all HMI models software easy to use remote program
$347.00 - $650.00
Min Order: 1 piece
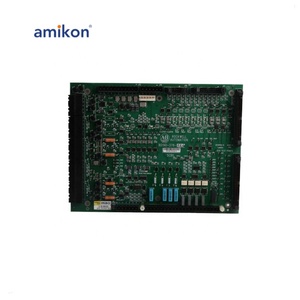
Competitive Price 80190-380-02-R Drive Board price plc controller for injection molding machine
$10.00 - $129.00
Min Order: 1 piece
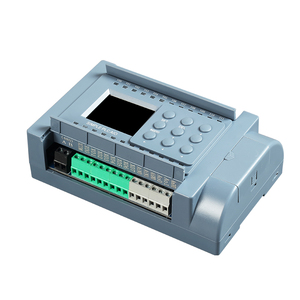
Huaqingjun PLC 8-in 8-out Relay Output 2-Channel Pulse Output All-in-one Machine Easy To Program PLC Controller for Servo Motor
Ready to Ship
$48.00 - $51.00
Min Order: 5 pieces
Shipping per piece: $4.61

100% new original plc controller FX3U-48MR/ES-A fx3u plc for mitsubishi
$90.00 - $130.00
Min Order: 1 piece
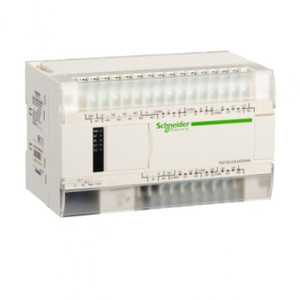
Original 100% Programmable logic controller TM218LDA24DRN TM218LDA16DRN TM218LDA24DRN TM218LDA40DRN PLC for Schneider
$100.00 - $200.00
Min Order: 5 pieces
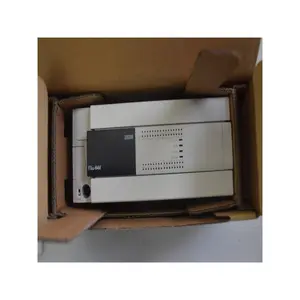
Industrial Automation Plc For Sale Cheap China Wholesale Chinese Plc Controller FX2N-48MT-ESS For Mistu
$254.97 - $311.63
Min Order: 1 piece

FuYanSheng IO-Link Industrial Ethernet fieldbus module Profibus-DP 003C11 8 IO ports Protection class IP67 for PLC controllers
$350.00 - $400.00
Min Order: 10 pieces
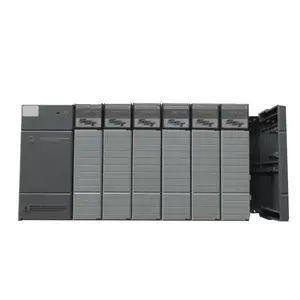
original plc control mini plc for sale 1788-CN2DN
Ready to Ship
$1,201.54
Min Order: 1 piece
Shipping per piece: $224.82
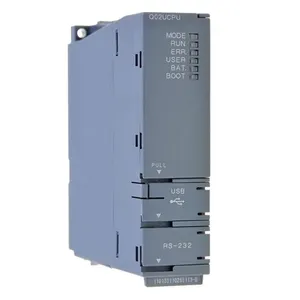
Q02UCPU Series PLC Controller New Original Warehouse Stock Plc Programming Controller for Q02UCPU
$60.00 - $100.00
Min Order: 1 piece
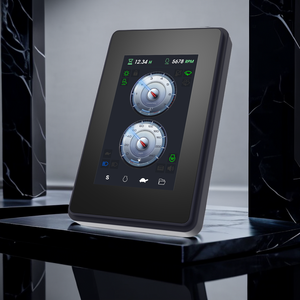
Plc Controller For Agriculture Automation Display And Control Terminal Industrial Display Capacitive Touch Monitor 4.3 Inch
$300.00 - $331.00
Min Order: 1 acre
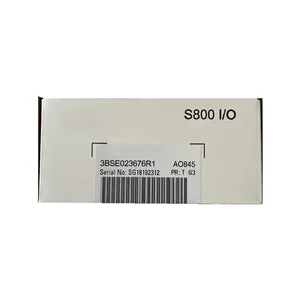
The best discount price PLC Controller AO845 3BSE023676R1 for A-s-e-a-B-r-o-w-n-B-o-v-e-r-i
$100.00
Min Order: 5 pieces

Profinet Remote Io Module Controller Module 32 Input / Output For Plc Controllers
$70.00 - $80.00
Min Order: 1 set

100% new original PLC Controller Q06HCPU High-Speed Module for mitsubishi
$50.00 - $70.00
Min Order: 1 piece

YAMATA original Controlador programable CJ1W-OD261 plc controller for injection moulding machine PLC
$139.00 - $144.00
Min Order: 1 piece

100% Brand Original 1762-L40BXB for 1200 plc controller best price in stock
Ready to Ship
$40.00 - $50.00
Min Order: 5 pieces
Shipping per piece: $191.48
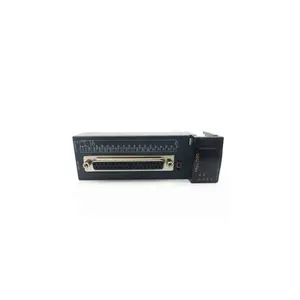
New Original PLC Controller G6Q-TR2B PLC for ls
$60.00 - $99.00
Min Order: 1 piece

High Quality AS228P-A Programmable Delta PLC Controller Famous Brand for CNC Lathe & Other PAC & Dedicated Controllers
$200.00 - $304.00
Min Order: 1 piece
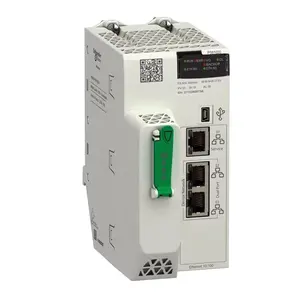
New and original PLC controller BMXDD06402K processor interface module for Schneider
$360.00 - $398.00
Min Order: 1 acre

High quality PLC controller 6ES7232-4HD32-0XB0 power module for Siemens
$100.00 - $340.00
Min Order: 1 piece
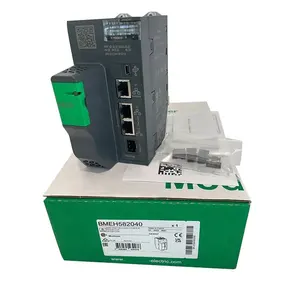
New Original BMEH582040 BMEH584040 BMEP581020 BMEP582040 HMI Touch Panel Screen PLC for Injection Molding Machine PLC Controller
$2,576.00 - $3,576.00
Min Order: 1 piece
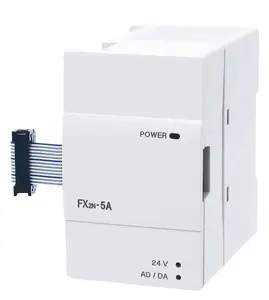
Melsec Mitsubishi's inverter module input/output module FX2N-5A for PLC controllers
$100.00 - $200.00
Min Order: 5 pieces
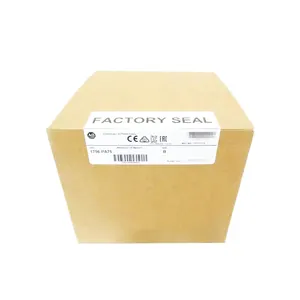
Spot Goods For New PLC Controller 1756-PA75 Power Supply Module 1756 ControlLogix Warranty 1 Year Best Price
$260.00 - $560.00
Min Order: 1 piece

100% original TM221C128UPAC module For PLC controllers
Ready to Ship
$99.00 - $299.00
Min Order: 1 piece
Shipping per piece: $47.43

Brand Delta Plc Expansion Module Plc automation Controller DVP12SA211T Sa2 Series Plc Controller DVP12SA211T For Air Compressor
Ready to Ship
$75.00 - $85.00
Min Order: 1 piece
Shipping per piece: $20.00

Fx5u-32mt/Es Mitsubishi PLC Controller for Industrial Automation
$50.00 - $100.00
Min Order: 1 piece
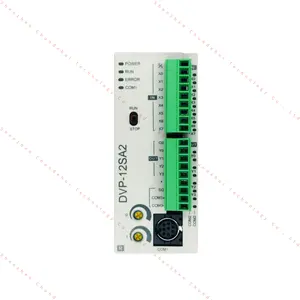
Best Price DVP Series PLC Controller DVP12SA211R for industrial control plc programming controller
$50.47 - $50.48
Min Order: 1 piece

Original ILC 171 ETH 2TX PLC Controller 2700975 for Phoenix
$550.00 - $650.00
Min Order: 1 piece

XIQIAN Siemens SIMATIC ET200SP 6ES7193-6PA00-0AA0 Spare Part Server Module For ET 200SP PLC Programming Controller Siemens
$50.00 - $70.00
Min Order: 5 pieces
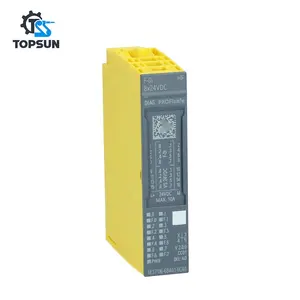
Industrial Controls 6ES7136-6BA01-0CA0 PLC controller SIMATIC DP electronic module for ET 200SP
$135.00
Min Order: 2 boxes
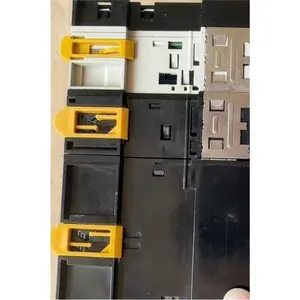
532P CJ1W-PA05 golden supplier plc controller for machine
$12.60 - $15.00
Min Order: 1 piece
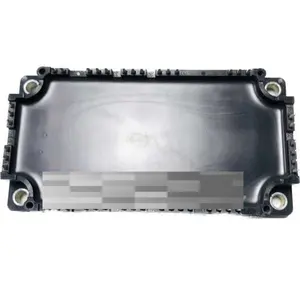
7MB150XNE10-507MB150VN10-50 golden supplier plc controller for machine
$7.60 - $9.00
Min Order: 1 piece
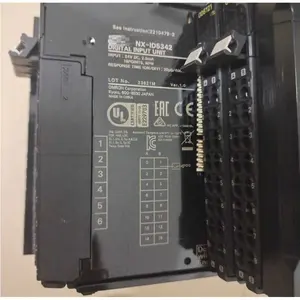
P NX1P-904DT-BA PF060/ ID54/OD511 golden supplier plc controller for machine
$46.60 - $51.00
Min Order: 1 piece
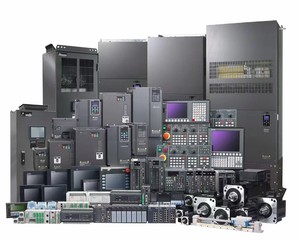
new original fx3u plc FX3U-48MR/ES-A plc controller for
$80.00
Min Order: 1 piece

6ES7331-7PF11-0AB0 Good Price for Brand Plc Controller 6ES7331-7PF11-0AB0
$122.00
Min Order: 1 piece