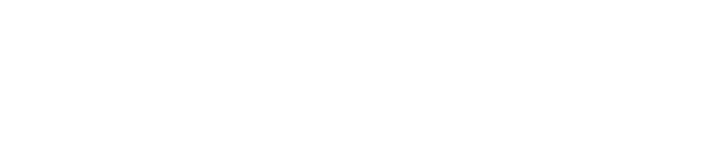

2023 Da53t Cnc Hydraulic Metal Sheet Plate Press Brake Hydraulic Press Brake Wc67k 40t 2500 For Bending Machine Price

High Quality Bending Machine Hydraulic Press Brake Metal Sheet Bending/folding Torsion Bar Machine

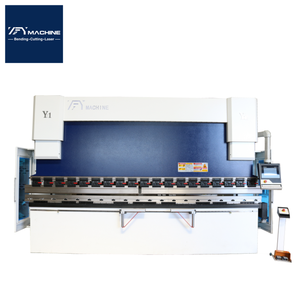
ZFY CNC Press Brake 6 Axis 135T/3200 Hydraulic Sheet Metal Bending Machine

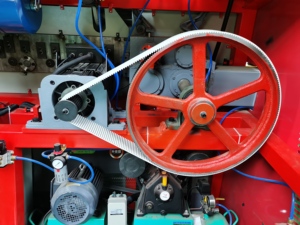
Customized 6-16mm Rebar Steel Rod Bar Stirrup Bender Bending Machine Automatic Rebar Bending Machine With Plate Reinforcement


Best Selling DA69T 2mm Stainless Steel Forming Hydraulic Cnc Bending Machine And 100T 2500 Press Brake Machine


Press Brake WC67K Series 100 Ton 3200 10 Feet Sheet Metal Bending Machine NC CNC Hydraulic Press Brake


2023 hot sale automatic bending machine price press brake cnc bending machine bending irons sheet metal cutting and bending mach

Automatic Integrated Metal Rule Die Steel Knife Bend Bending Machine Auto Knife Sheet Blade Bender Cutting Machine Price

300 Ton 100T 3200 Hydraulic CNC MS Iron Steel Sheet Metal Plate Bending Machine Price

factory price CNC stainless steel bending machine price 6mm metal plate press break hydraulic metal sheet press brake
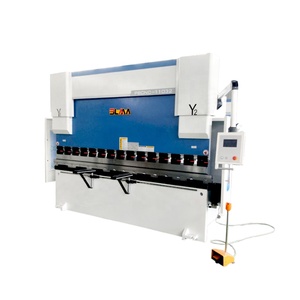
160T 3200 4000 Sheet Metal Servo Hydraulic CNC Press Brake Bending Machine Price

Rbqlty-High quality CNC Bending machines Hydraulic low price iron Sheet Metal 100 125 Ton folding press brake machine

Good Price Da69t Hydraulic Servo Aluminium Profile Cnc Bending Automatic Sheet Metal Bending Machine Servo Press Brake Machine
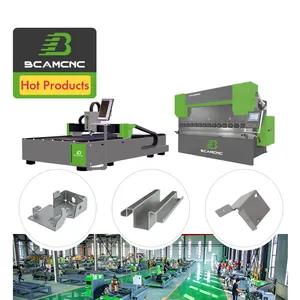
automatic copper hand operated bending machine cnc sheet bending machines prices laser cutting machine
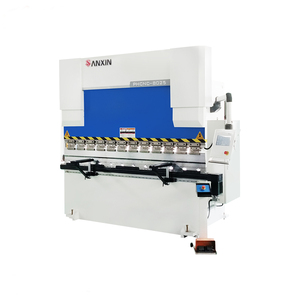
Heavy shearing folding copper automatic sheet cnc metal stainless steel plate hydraulic bending machine price

China Genuo brand 2000mm cnc hydraulic press brake stainless steel sheet bending machine price

CNC 7+1 Axis 110t/3200 Press Brake Sheet Metal Bending Machine DA66T delem press brake machine price

DELEM DA53T Wc67k We67k 200T 3200mm Plate Metal Sheet Hydraulic CNC Press Brake Machine small 10mm Price Manual Bending Machine

Good price hand type sheet metal folder machine/manual plate edge bending

JDCbend 3200E Pneumatic Magnetic Folding Machine, Electromagnetic Sheet Metal Bending Machine Price

30T/1600 factory direct sale good price customized sheet metal Mini small automatic cheap press brake bending machine
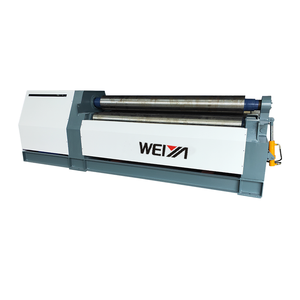
Good Price 4 Rolls Hydraulic Plate Steel Sheet CNC Roller Bending Machine
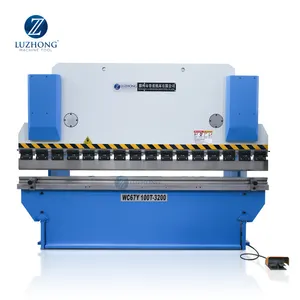
Manual Sheet Metal Bender Price WC67Y 63T Steel Bending Machines
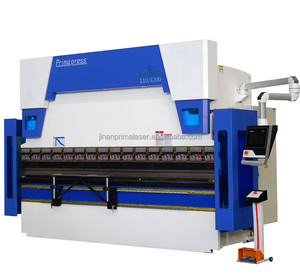
2023 Prima Custom Factory Direct Lowest Price Hydraulic Press Brake CNC Sheet Metal Folding Bending Machine

Manual magnetic sheet metal bending machine high quality low price

best CNC stainless steel bending machine price 5mm plate press break hydraulic metal sheet press brake

Good Price bending sheet machine Hydraulic Metal Steel Press Brake Machine with CNC system

Magnetic Folding Machine, Electromagnetic Sheet Metal Bending Machine Price Magnabend 3200E

best price cnc automatic press braking sheet metal bending machines

Factory Outlet Price Replaceable Tools Die CNC MG-1003 Press Brake Hydraulic Metal Sheet Bending Machines

China Supertech 4 Rolls Hydraulic Plate Steel Sheet Bending Machine Roll Cnc Metal Rolling Machine price

LOW PRICE sheet bending machines Metal Folding Machine from PREDA
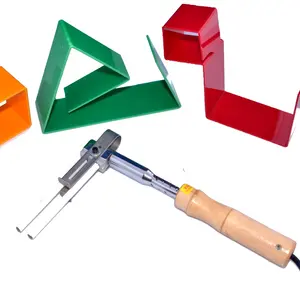
120mm Acrylic sheet bending machine cheaper price 110v 220v-240v 50w adjustable temperature

Electric Servo wc67y 3200mm sheet metal hydraulic press brake 80t CNC bending machine price

nice price sheet bending machines used in tanks fabrication
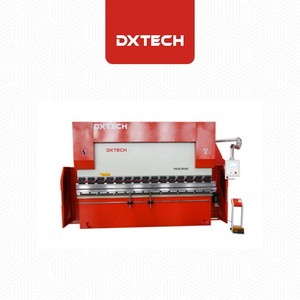
Dxtech New Style CNC Metal Other Bending Machines Sheet hydraulic Bending Machine Price Panel Press Brake

Factory Price 110T2500 Steel Sheet Motor Hydraulic Bending Machine Press Brake Machine

NO POLLUTION hand type sheet metal folding machine manual plate bending machine price

WILACNC Bending machine Factory Price 30t 40ton 2000mm Plate Press Brake Hydraulic Metal Sheet Press Brake
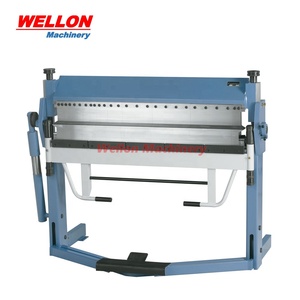